Alta Vista Solutions reduced costs on bridge inspection reporting by 75% by using Data Recon
Updated: Aug 11, 2020
For this case study we interviewed Bahjat Dagher, Vice President at Alta Vista (www.altavistasolutions.com) about the significant savings in time and money the company has experienced since they began using Data Recon for their electronic data collection, reporting and management.
Bahjat manages various inspection and material testing contracts for Alta Vista. He also performs various functions in operations, business development and recruitment initiatives. Alta Vista conducts hundreds of bridge inspections yearly. To date, they have used Data Recon on 60 bridges and 16 stations.
BEFORE DATA RECON
In-field Data Collection
Traditionally, two bridge inspectors in the field inspect a bridge or structure for defects such as cracks, corrosion, distortion, exposed rebar, delamination, etc. Once a defect is identified it is marked on the bridge itself and three photos of each defect are taken using a digital camera.
Reporting
Once they return to the office, the pictures are downloaded to a desktop computer. The inspector then must painstakingly go back through the photos and attribute each series of images to a specific defect. Then they build their report in Word. The photos must be cut and pasted to accompany each defect listed in the report. This process is laborious and prone to errors. On average, a report for a single bridge or structure takes 16 hours.
Data Management
Next, if any sort of data management is needed such as grouping defects by date, priority or any other form of diagnostic, the complexity of such process when done manually increases exponentially.
WITH DATA RECON
Data Collection
Using Data Recon’s field inspection app, a bridge inspector can instantly capture a defect using a tablet and specify its type from a drop-down menu optimizing the inspector’s time in-field. Each defect captured has a picture and type automatically linked. According to Isaac Harris, Bridge Inspector at Alta Vista, the ease of capturing defects with Data Recon and the fact that they don’t have to worry about picture editing and matching at the office, is enabling them to capture six times the number of pictures and provide richer reports. Isaac also said that using the in-field app is quite easy. He was able to train a fellow bridge inspector in approximately three days.
Reporting
As soon as the field inspection is complete, a report is automatically created. The report is in a Word document which Bahjat and his team customize as they please. Using Data Recon, Alta Vista managed to expedite their reporting time by 4, reduce their reporting cost by 75% and reduce their overall inspection time by 30% for each inspection. Isaac adds that that they can take advantage of the time saved to potentially double the number of bridge inspections that they can conduct in a day.
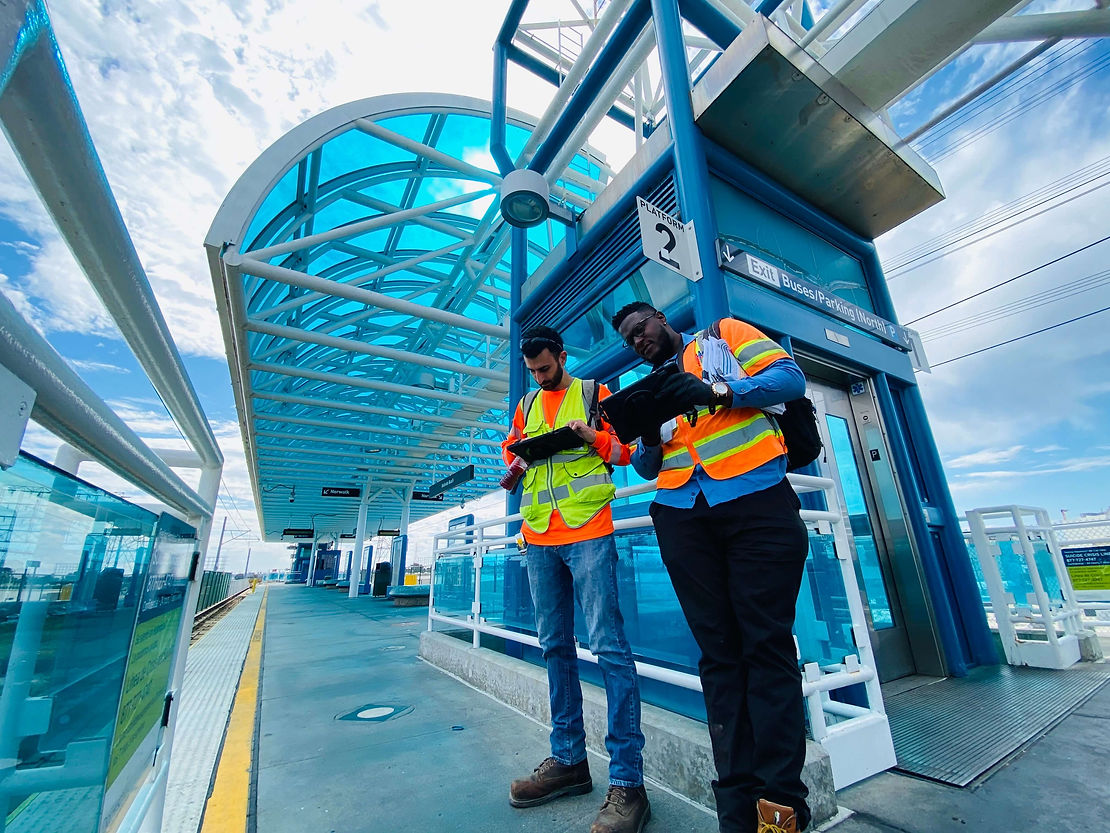
“We reduced our reporting time from 16 hours to 4 hours”
Bahjat Dagher, VP Alta Vista
Data Management
In addition to time and money savings, Alta Vista is now capable of providing a complete Defect Database to their clients through the Data Recon portal. This Defect Database enables their client to sort all reported defects from all structures based on various criteria, such as condition state, in order to identify the items that need immediate attention. In addition to the defect database, Alta Vista’s clients now have the capability to track inspections and monitor defects captured in real time as opposed to the traditional once per year thanks to Data Recon.
Bahjat concluded by thanking the Data Recon team for enthusiastically acting on feedback, accommodating requests and creating solutions for tailored to specific problems.